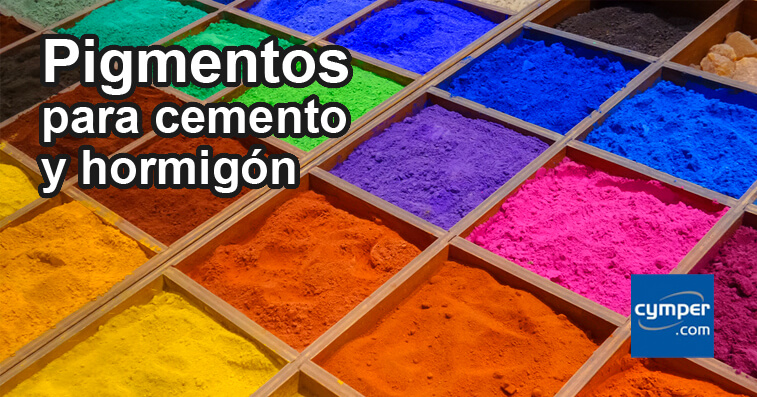
Un pigmento es una sustancia insoluble que añadidas a cementos u hormigones, le confieren color. Los más habituales son los óxidos de hierro para conseguir tonos rojos, amarillos o negros, y todas sus mezclas como los naranjas y marrones. Con los óxidos de cromo se consiguen tonos verdes y con los óxidos de cobalto se logran los tonos azules.
INDICE
- Pigmentos, colorantes Y NOCIONES DEL COLOR
- ORIGEN DE LOS PIGMENTOS
- NATURALEZA DE LOS PIGMENTOS
- PARTICULAS, AGREGADOS Y AGLOMERADOS
- LIGANTE Y DISPERSION DE UN PIGMENTO
- PIGMENTOS APROPIADOS PARA PRODUCTOS ELABORADOS A BASE DE CEMENTO Y/O CAL 10
- ASPECTOS QUE INFLUYEN EN LA COLORACIÓN
- PRESENTACIÓN DEL PIGMENTO
- PATOLOGIAS SUPERFICIALES INHERENTES A MORTEROS Y HORMIGONES Y SU INFLUENCIA SOBRE LAS PROPIEDADES DECORATIVAS. EFLORESCENCIAS Y DESTONIFICACIÓN.
- Las eflorescencias
- Actuaciones sobre el agua para reducir las eflorescencias
- Actuaciones sobre el hidróxido cálcico para reducir las eflorescencias
- Destonificación
- Las eflorescencias
- LEGISLACIóN
I. PIGMENTOS, COLORANTES Y NOCIONES DEL COLOR
Una parte de los usuarios suele utilizar la denominación de “colorante” para referirse al producto que colorea el mortero, sin embargo, su descripción correcta es la de pigmento [1].
Un colorante es aquella sustancia soluble en un medio o vehículo (normalmente acuoso) que por sus propiedades ópticas colorea dicho medio a menudo reaccionando con él. Por ser solubles, limita su aplicación a productos alimenticios principalmente. Su naturaleza es casi siempre orgánica, y puede ser de origen natural o sintético.
Un pigmento sin embargo, es una sustancia insoluble. La forma y tamaño de sus partículas le confieren unas propiedades ópticas tales que la luz que reflejan es muy intensa. Por supuesto, si cambiamos el iluminante, es decir la longitud de onda de la luz, las propiedades ópticas se modificarán. Por tanto, las sustancias que añadimos a un producto cementoso para conferirle un color, son los pigmentos.
El color que percibimos de los objetos es fruto de una interpretación de nuestro cerebro a un estímulo del ojo al recibir la luz reflejada por un objeto que está siendo iluminado [2].
La luz solar blanca como sabemos se compone de varias longitudes de onda que constituyen el espectro visible. Cada franja de longitudes de onda determina un color. Podemos conseguir descomponer la luz blanca en una serie de colores al hacerla pasar por un prisma. El arco iris surge por la descomposición que experimenta la luz blanca al atravesar la gota de agua, que actúa como un prisma. Nuestro ojo es sensible solo a los colores cuya longitud de onda esta aproximadamente entre 400 y 700 nm (espectro visible), los ultravioletas (por debajo de 400) y los infrarrojos (por encima de 700) no podemos verlos.
Un objeto negro es el que no refleja ningún color, es decir, absorbe todas las longitudes de onda de la luz blanca. Asimismo, un objeto verde, absorberá todos los colores de la luz blanca excepto el verde.
Para colorear los productos a base de cemento tenemos las limitaciones que nos marcan las tonalidades de los pigmentos que podamos emplear. Como los óxidos de hierro (amarillos, rojos y negros) ocupan un lugar hegemónico en este caso y las opciones de azul son prohibitivas, normalmente encontraremos en el hormigón los tonos puros del óxido de hierro o sus combinaciones. También en menor medida los verdes de óxido de cromo [3], [4].
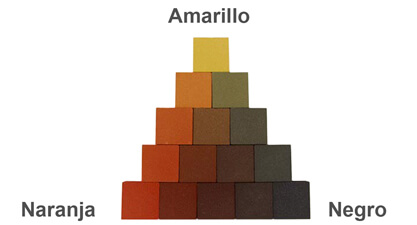
Echemos un vistazo a las tonalidades que se pueden conseguir con los mencionados pigmentos de óxido de hierro:
- Amarillos con tonalidades más o menos rojizas, pero sin grandes variaciones entre los distintos grados.
- Rojos con tonalidades que van desde tonos muy anaranjados hasta violetas pasando por rojos más o menos azulados.
- Negros con tonalidades desde rojizas a azuladas, pero como ocurre en el caso de los amarillos, sin grandes diferencias. En realidad, con los negros de óxido de hierro solo podemos conseguir en los productos de cemento tonos de gris. Un negro de verdad solo se podrá conseguir con el empleo de un pigmento de negro de humo [5].
- Marrones o pardos. Como mínimo se van a componer de rojo + negro. Cuando se persiguen tonalidades cuero o madera, se añade también amarillo. La gran variedad de tonalidad bien diferenciada que hay entre los rojos, hace casi infinita las posibilidades. A veces también se recurre a utilizar en la misma mezcla más de un tipo de rojo. Con naranja y cemento gris también se obtienen marrones.
- Naranjas o salmones. Se obtienen mediante la combinación de amarillo como color mayoritario y rojos.
- Verde. Se puede conseguir una tonalidad apagada y sucia añadiendo pequeñas cantidades de negro al amarillo, o simplemente usando amarillo con cemento gris.
II. ORIGEN DE LOS PIGMENTOS
Los pigmentos pueden ser naturales o sintéticos.
Los naturales son productos de cantera o mina. Se tratan para eliminar parte de las impurezas y se muelen finamente, o simplemente se muelen sin tratamiento previo. Son conocidos como óxidos naturales, tierras colorantes o simplemente ocres.
Hasta muy avanzado el siglo XIX eran los únicos disponibles. Los casos más antiguos conocidos de su utilización por el hombre los tenemos en las pinturas rupestres (aquellas en las que se utilizaron óxidos de hierro, aún se conservan). Tierras colorantes legendarias que marcaron una época son los Sienas de Italia y Francia, ocres de Vaucluse o Nièvre, sombras de Chipre, Italia y Francia y rojos de España [6].
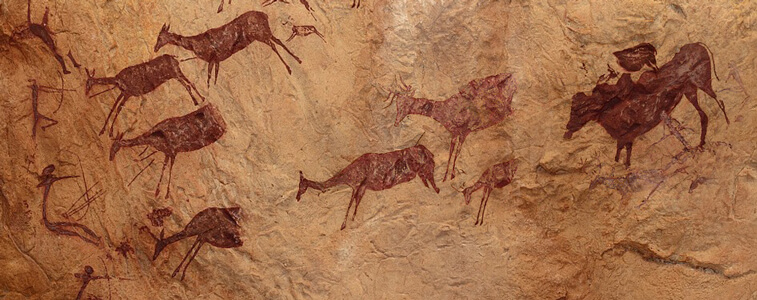
ligantes de origen natural.
A finales del siglo XX la mayoría de las explotaciones tradicionales en Francia, Italia y España fueron clausuradas. Hoy en día su uso ha quedado muy restringido debido a que el precio se va aproximando al de los sintéticos, su fuerza colorante es baja, los tonos son sucios amarronados en comparación con los sintéticos y su riqueza y tono están sometidos a fluctuaciones.
Los pigmentos sintéticos son aquellos que se obtienen después de determinadas reacciones químicas partiendo de unas materias primas iniciales. Su desarrollo parte de finales del siglo XIX y principio del XX primeramente con más protagonismo en Inglaterra y después en Alemania.
III. NATURALEZA DE LOS PIGMENTOS
Los pigmentos podrán ser de naturaleza orgánica: moléculas que contienen carbono formando enlaces covalentes carbono-carbono o carbono-hidrógeno, y de naturaleza inorgánica: los que no poseen dicha composición.
Los orgánicos se suelen caracterizar por:
- Peor solidez a la luz, ácidos y álcalis.
- Elevada fuerza colorante.
- Tonos limpios.
- Dispersión más complicada que en los inorgánicos.
- Pocos mantienen su estabilidad por encima de los 200 ºC.
- Tamaños de partícula muy pequeños en comparación con los inorgánicos.
Los inorgánicos se suelen caracterizar por:
- Buena solidez o resistencia a la descomposición por la radiación ultravioleta.
- Buena resistencia a los ácidos y álcalis.
- Modesta fuerza colorante.
- Buen poder cubriente. También se dice buena opacidad.
- Tonos poco limpios en comparación con los pigmentos orgánicos.
- Facilidad de dispersión.
- Suelen tener más resistencia a la temperatura que los orgánicos.
IV. PARTICULAS, AGREGADOS Y AGLOMERADOS
Las partículas son las unidades más pequeñas de un pigmento y como se ha dicho son las responsables de las propiedades ópticas de este. Estas se forman al ordenarse los diminutos cristales originados durante la obtención del pigmento. Los tamaños de partícula habituales de los pigmentos inorgánicos utilizados en la coloración de productos de cemento están entre 0,09 y 0,8 μm
Las partículas, en grupos de varias unidades forman agregados de partículas. En la mayor parte de las aplicaciones del pigmento estos agregados no se llegan a separar. El tamaño de estos agregados puede llegar a ser de unas pocas micras. Como dato, el tamaño medio del cemento es cuando menos unas diez veces mayor que estos agregados [7].
Finalmente, cuando en el proceso de obtención del pigmento, este es secado, los agregados se van uniendo unos con otros formando los aglomerados, que alcanzan gran tamaño. La posterior molienda suele reducir el tamaño de estos aglomerados normalmente por debajo de 45 micras, siendo este el tamaño del polvo que recibe el consumidor.
Si en lugar de usar una molienda clásica tipo pendular o de martillos, se emplea el chorro de vapor sobrecalentado y presiones del orden de 1,47 Megapascales o bien aire comprimido (molienda Jet) se puede llegar casi a la total desaglomeración, y entonces llamaremos al pigmento “micronizado”, pero el mayor precio de estos productos solo se valora y justifica en aplicaciones como determinados tipos de pinturas y plásticos en donde se percibe una mejora en la facilidad de dispersión y a veces en otras características.
Cuando los pigmentos se envasan, debido a su estructura amorfa y propiedades cohesivas, los aglomerados se enganchan unos con otros formando nuevos aglomerados de mayor tamaño y terrones. Aunque estas entidades se disgregan con facilidad, el producto tiene mala fluidez y una enorme tendencia a formar bóvedas. A esto último también contribuye la facilidad para atrapar aire y la dificultad para soltarlo, es decir, que tendrán una densidad aparente variable según el estado de agitación o empaquetado. Esto representa un gran inconveniente para las instalaciones de dosificación automática y en general para la manipulación, mezcla, envasado y transporte mecánico.
V. LIGANTE Y DISPERSION DE UN PIGMENTO
Siempre que aplicamos de un pigmento, subyacen por un lado las características del ligante, y por otro la dispersión de dicho pigmento en el ligante.
El ligante tiene la misión principal de mantener unidos el conjunto de elementos base y aditivos que forman un material:
- Para una pintura, el ligante es la resina.
- Para un plástico, será el polímero.
- En un aglomerado asfáltico o mezcla bituminosa, es el betún.
- Y en un mortero u hormigón será el cemento y/o la cal (ligantes hidráulicos).
El pigmento, como ocurre con otros aditivos y componentes de la mezcla, debe alcanzar un nivel de disgregación de los terrones formados durante el almacenaje, incluso llegar más allá desaglomerándose y difundiéndose de manera homogénea con todos los demás componentes. Esta dispersión se consigue mediante una agitación del conjunto con un mayor o menor efecto cortante.
En el caso de los morteros y hormigones, esta energía mecánica se produce durante el mezclado o amasado. En un hormigón, en donde abundan los áridos de tamaño variado el esfuerzo de cizalladura es muy intenso y la dispersión se puede considerar completa. Puede presentarse alguna deficiencia en la dispersión en los morteros de muy baja granulometría de los áridos o muy ricos en impalpables tales como estucos y microcementos. En este caso puede ocurrir que:
- Se reduzcan las posibilidades de desarrollo de color del pigmento, por lo que no aprovechamos la totalidad del mismo.
- Especialmente en amasadas semisecas y cuando estas son de pequeño tamaño, parte de estos aglomerados de pigmento, cuyo tamaño inicial es inferior a 45 micras y los terrones pueden rotar sin cizallarse en algunas zonas de la amasadora pudiendo llegar a formar “bolitas” de varios milímetros de diámetro envueltos por una débil capa de cemento o árido impalpable. Aquellas bolitas que quedan en la superficie de la pieza formada, se pueden romper dejando manchas intensas en la superficie de forma circular y un cráter (ver imagen). También pueden surgir las llamadas “colas de cometa” o ráfagas cuando se ha talochado, es decir, alisado por fricción superficial, o enrasado.
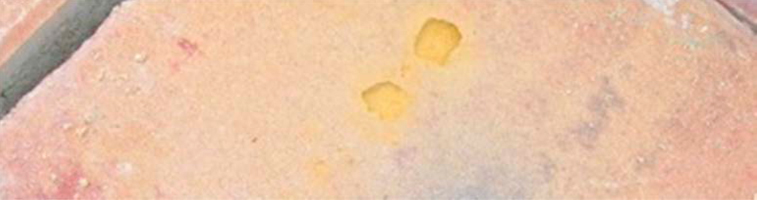
Las dosis de pigmento siempre deber prepararse por peso, nunca por volumen, ya que debido a la variación de volumen que el pigmento en polvo puede experimentar podríamos cometer errores en la dosificación de una amasada a otra. Incluso cuando los pigmentos se presentan en forma granular o líquida la dosificación se suele hacer por peso.
Los pigmentos se suministran de forma estándar en sacos de 20 o 25 Kg. (Ver imagen), pero bajo solicitud es posible adquirirlos en dosis adecuadas a necesidades concretas. Además, estas dosis preparadas también pueden suministrarse en envases hidrosolubles, con lo que se evita el contacto con el pigmento (Ver imagen).
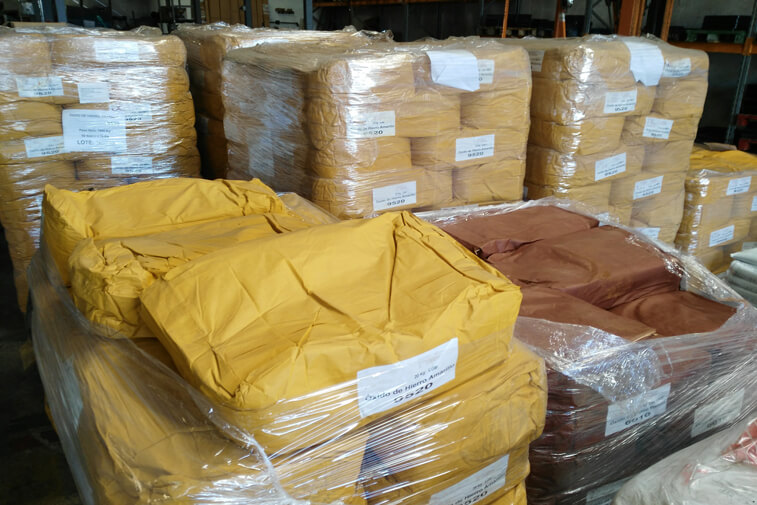
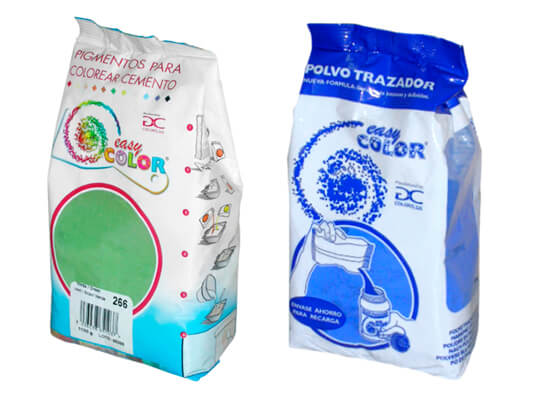
Para asegurar una adecuada dispersión del pigmento, será conveniente respetar unas pautas en el proceso de amasado. Lo ideal sería hacer una pre mezcla seca de los áridos, pigmento y cemento. Después se añadiría el agua y procederíamos a un amasado final.
Lo anterior es la forma con la que se opera con los morteros y hormigones secos, en donde las mezclas son producidas en planta y el agua se añade en obra procediendo
el amasado final justo antes del consumo.
Para la elaboración de un mortero y hormigón húmedos, ya sea en planta o a pie de obra, se puede recomendar la siguiente secuencia:
- Con la mezcladora en movimiento verter preferentemente el árido grueso o también todas las fracciones de árido. En caso de usar pigmentos en forma granular, será necesario que estos áridos contengan en torno al 10% de humedad, añadiendo agua si es necesario. Esto se debe a que estos pigmentos en forma granular requieren para disgregarse además de esfuerzo de cizalladura, cierta cantidad de agua para disolver el aglutinante que contienen.
- A continuación verter la dosis de pigmento en cualquiera de sus formas, polvo, granular o líquido. De ser posible de forma progresiva y continuar la agitación. Si se añaden aditivos en forma de polvo, también se vierten en este momento.
- Después de un tiempo que dependerá del tamaño de los áridos y de las características de la mezcladora, verter el cemento dando un tiempo similar al anterior.
- A continuación verter los áridos finos e impalpables en el caso de no haberlos vertido en el punto 1º. Dejar otro corto periodo en agitación.
- Finalmente añadir el agua y otros aditivos líquidos. Se mantiene la agitación un mayor tiempo que los anteriores.
En una planta de hormigón en la que el amasado se hace en el camión hormigonera, el vertido del pigmento debe hacerse preferentemente sobre la cinta que transporta los áridos.
Para un mortero seco, la secuencia es la siguiente:
- Fracción gruesa de los áridos.
- Pigmento y dar un tiempo suficiente de agitación
- Cemento
- Áridos finos e impalpables.
Para un microcemento y en general en amasadas pequeñas o con mezcladora poco eficaz puede ser apropiado batir el pigmento en parte del agua de amasado y después verter esta emulsión al mortero que previamente se habrá amasado con el resto del agua.
Cualquier otro método puede ser válido si se verifica la adecuada dispersión del pigmento.
VI. PIGMENTOS APROPIADOS PARA PRODUCTOS ELABORADOS A BASE DE CEMENTO Y/O CAL
Los pigmentos orgánicos, si bien en algunas ocasiones se utilizan, como los azules se Ftalocianina tratados con humectantes, no son estables por su mayor reactividad unas veces, por el reducido tamaño de su partícula, o su baja resistencia a la intemperie, que es el principal lugar donde se aplica color a los morteros y hormigones.
Estos pigmentos terminan transformándose en otros compuestos sin propiedades pigmentarias o migrando a la superficie, por lo que unos tonos iniciales a veces bastante espectaculares terminan desapareciendo casi por completo después de algún tiempo.
Serán por tanto los pigmentos inorgánicos, si bien no de forma general, los que mantienen la estabilidad en los morteros y hormigones.
Los pigmentos adecuados deben tener:
- Resistencia elevada a los álcalis (el cemento y la cal son de naturaleza alcalina).
- Resistencia a la acidez, pues muchos elementos de cemento se pueden encontrar sometidos a condiciones ambientales de cierta acidez.
- Resistencia a la radiación solar.
- Ser compatibles con los sistemas acuosos, ya que los morteros y hormigones necesitan agua para fraguar.
- Tener un tamaño óptimo que asegure un buen anclaje en la estructura del mortero u hormigón.
Con todo lo anterior podemos establecer la siguiente tabla donde relacionamos los principales pigmentos utilizados para colorear morteros y hormigones:
TABLA 1. Principales pigmentos utilizados en productos cementosos.
COLOR | PIGMENTOS |
Blanco |
|
Amarillos |
|
Rojos |
|
Negros |
|
Verdes |
|
Azules |
|
Marrones y Naranjas |
|
VII. ASPECTOS QUE INFLUYEN EN LA COLORACIÓN
Mediante la dosificación del pigmento podemos obtener tonos pasteles con adiciones por debajo del 0,5%, hasta la propia saturación como es el caso de los pavimentos continuos fratasados donde nos moveremos entre el 10 y el 15%.
Cabe mencionar que aparte de otros parámetros como la resistencia, plasticidad, porosidad, etc., desde el punto de vista del color, usar cemento blanco o gris, la granulometría de los áridos, relación agua/cemento, vibrado, prensado, fratasado, extrusionado, etc., van a afectar de manera relevante a la coloración del mortero u hormigón [8].
Mencionaremos a continuación algunos detalles:
- Cemento blanco/gris. El cemento blanco proporcionará tonos más luminosos que el gris, a la vez que más abanico de tonalidades. Los cementos grises, limitan los colores claros como amarillos y azules principalmente, quedando estos con tonos muy apagados y oscuros. Sin embargo para los tonos oscuros (rojos, negros, marrones) la diferencia entre usar cemento blanco o gris es más reducida a nivel de color.

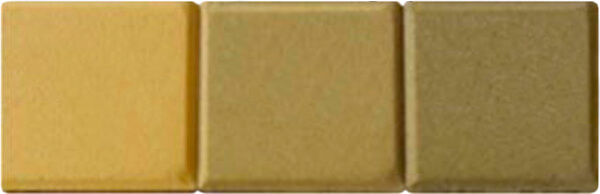
Izquierda: cemento blanco. Centro: cemento gris oscuridad intermedia. Derecha: cemento gris oscuro.
- Granulometría de áridos o porción total de “finos”. Un preparado muy rico en finos va a necesitar más dosificación de pigmento ya que la superficie específica total es muy superior a la de un preparado de granulometría más gruesa, y por tanto hará falta más cantidad de pigmento para cubrir dicha superficie.
- Relación agua/cemento. Según la consistencia deseada, la cantidad de agua será variable. Al aumentar esta, los tonos se aclaran. El exceso de agua en el preparado genera en el enrase un sobrenadante superficial débil constituido por arrastre de pigmento, finos, y diversos elementos del mortero u hormigón, con lo que el valor estético podría verse mermado. También el exceso de agua va a provocar que, cuando esta desaparezca por evaporación, deje infinidad de micro poros que distorsionan el efecto cromático del producto pigmentado rebajando la intensidad de su tono. Esto se debe al aire ocluido en los poros que aporta matiz blanquecino.
- Color de los áridos. Su influencia es menor en el color final, ya que el aporte de superficie específica es bajo en relación a la del cemento. Los áridos son envueltos por lechada de cemento, por lo que su tonalidad tiene un impacto bajo en el color final.
- Textura superficial y tratamiento que realce el brillo superficial. Una superficie brilla más cuanto más lisa es. Si además se aplica un recubrimiento a base de resinas, este brillo se potencia de forma importante a la vez que sellamos los poros evitando la oclusión de suciedad que terminaría matizando el producto.
- Tratamiento mecánico durante la fabricación. Vibrado y prensado tienen más efecto sobre la resistencia que sobre el color ya que lo principal es compactar. Sin embargo, la extrusión y talochado aportan una superficie más perfecta, con menos irregularidades, lo que se traduce en un tono alto y con más brillo.
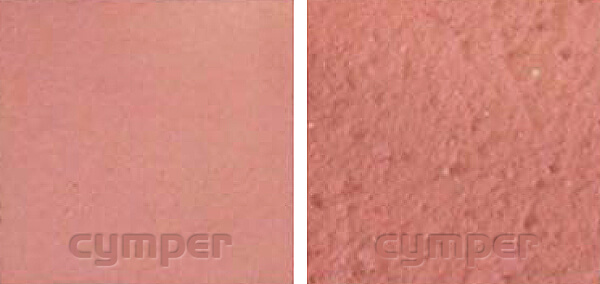
- Tratamiento mecánico superficial postfraguado. Fresado, granallado, abujardado aportan una combinación entre el árido que queda a la vista con su color natural y el mortero pigmentado que lo envuelve.
- Tratamiento químico superficial inhibidor de fraguado. Mediante la impregnación de los moldes o el uso de sustancias retardantes de fraguado se puede conseguir un efecto de contraste entre árido y el mortero.
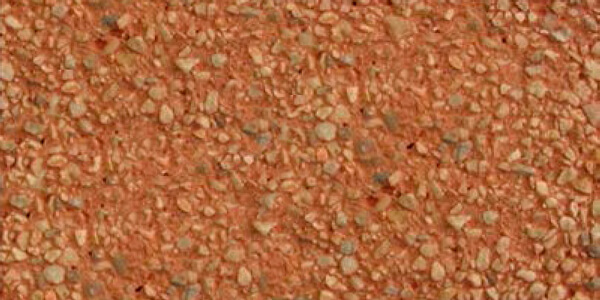
- Tratamiento químico superficial postfraguado. Un lavado con ácido diluido desintegra la capa más externa del producto, y tras el obligado enjuague para eliminar restos de acidez, tendremos bellas texturas que muchas veces solo un experto reconoce como producto artificial en lugar de piedra natural. Se produce un contraste entre el cemento pigmentado y el árido que ha perdido la cubrición.
En la Tabla 2 podemos ver tres probetas correspondientes a morteros en los que se mantienen la relación cemento-árido y la dosificación del pigmento amarillo ChromaFer 9520 al 3% respecto del cemento, pero se ha variado la relación a/c y el contenido en finos impalpables. En el caso de consistencia plástica (relación a/c=0,7) se muestra el aspecto en la cara de encofrado y en la de enrase.
Podemos ver que la pieza vibroprensada tiene la tonalidad más intensa debido a una reducida cantidad de agua de amasado y carencia de impalpables en el árido. En las piezas de colada vibrada, vemos que en las caras de encofrado, en la de la derecha la intensidad es más baja debido a un aumento considerable en el contenido en impalpables por parte del árido. Sin embargo, en las caras de enrase prácticamente no hay diferencia entre estas dos piezas de colada. Ello se debe a que la influencia del agua de amasado depositada en el enrase tras el vibrado afecta mucho más en el color final que el diferente contenido en impalpables.
TABLA 2. Influencia de la relación agua / cemento y contenido en impalpables.
Consistencia | Granular | Plástica | |
Fabricación | Vibroprensada | Colada vibrada alisada en enrase | |
Relación Agua / Cemento | 0,3 | 0,7 | 0,7 |
Superficie específica cm2/gr | 2900 | 2900 | 5800 |
Relación cemento / árido | 0,33 | 0,33 | 0,33 |
VIII. PRESENTACIÓN DEL PIGMENTO
- Pulverulenta. Todos los pigmentos se presentan originalmente en polvo. Sin embargo, a lo largo del tiempo, para mejorar la dosificación automática y a la vez mantener espacios de trabajo más limpios y salubres, algunos fabricantes han desarrollado y ofertado otras presentaciones.
- Líquido, slurry, pasta o suspensión acuosa. Surge a primeros de los 80. La teoría es que esta presentación se dosificará y dispersará mejor. Sin embargo tiene en contra:
- Un coste mayor pues para su elaboración se parte del polvo.
- Un transporte más caro, pues no es común que la preparación pigmentaria contenga más del 50-60 % en pigmento, siendo el resto agua y aditivos.
- Es sensible a prolongado almacenaje. El consumo preferente es de 6 meses.
- Asimismo, cuando los áridos a utilizar están húmedos (como ocurre muchas veces con el cuarzo en la fabricación de adoquines), no es necesario añadir agua para el amasado, con lo que utilizar este tipo de presentación puede provocar un exceso de agua.
Una variante fue la preparación de la emulsión en casa del cliente. Esta se almacena en tanques de poca capacidad con agitación constante, y desde ahí se van alimentando las mezcladoras. Sin embargo, problemas de falta de homogeneidad han hecho que cada vez se utilice menos. Recientemente algunos fabricantes de maquinaria de dosificación ofertan instalaciones que se nutren de producto en polvo suministrado en big-bags el cual es dosificado en un tolvín de pesaje en el que se ha vertido previamente cierta cantidad de agua. El tolvín incorpora un agitador. Finalmente el producto es bombeado hasta la amasadora.
- Granulado. Esta presentación apareció en los 80, y se obtienen por spray drying (secado por pulverización, también llamado atomización). Se trata de unas micro-esferas con un tamaño medio de 300 micras y que pueden fluir igual que el contenido de un reloj de arena. Se obtienen partiendo del polvo el cual se somete a un proceso de emulsión acuosa con sustancias aglutinantes. Finalmente el producto es pulverizado en torres de secado. Este producto se puede suministrar en big-bags los cuales se descargan sin dificultad alguna. A continuación, es transportado por aire en fase densa a través de tuberías después de ser pesado en un tolvín de pesaje. Para la correcta disgregación de estos micro gránulos es necesario durante el amasado, una fricción importante en presencia de algo de agua. Estos productos funcionan satisfactoriamente en hormigones semisecos como son los utilizados para la elaboración de prefabricados de adoquín, bloques y tejas. En el resto de aplicaciones presentan inconvenientes y por tanto se continúa utilizando el polvo.
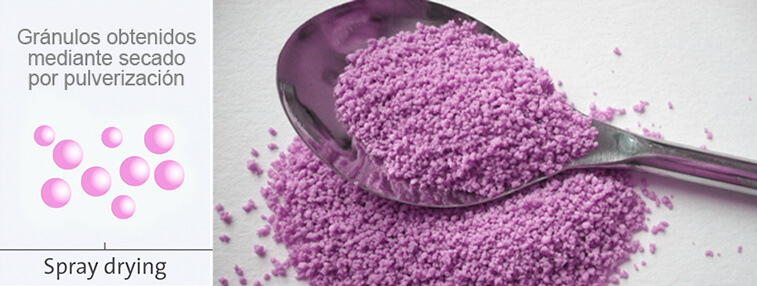
- Compactados. Una presentación pseudogranular surgió a finales de los 90. Es un producto similar al granulado spray drying, pero más económico en su proceso de obtención. Las ventajas e inconvenientes de estos productos son similares a los de los granulados, si bien fluyen algo peor y contienen algo de polvo.
IX. PATOLOGIAS SUPERFICIALES INHERENTES A MORTEROS Y HORMIGONES Y SU INFLUENCIA SOBRE LAS PROPIEDADES DECORATIVAS. EFLORESCENCIAS Y DESTONIFICACIÓN.
Podemos mencionar como más destacadas:
1.- Las eflorescencias
Este es un fenómeno molesto que consiste en la aparición de depósitos de carbonato cálcico en la superficie. Como estos depósitos son de color blanco, el impacto será mayor en las piezas de hormigón de colores oscuros, reducido en tonos claros y despreciable en los blancos.
Para que esto ocurra es necesario que flujos de agua transporten desde el interior de las piezas de hormigón hasta la superficie algunos elementos. Por tanto, tenemos unas eflorescencias primarias que ocurren principalmente durante el fraguado y otras eflorescencias secundarias que surgirán posteriormente por la lluvia o agua de los soportes en la medida que la pieza de hormigón sea más o menos impermeable.
Eflorescencias primarias
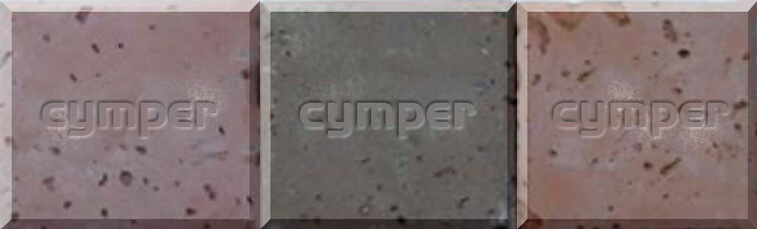
Eflorescencias secundarias
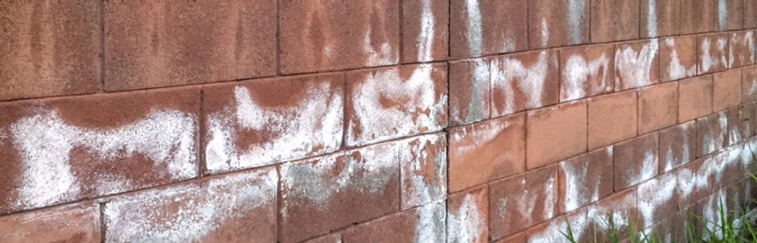
El proceso de formación de estos depósitos es el siguiente:
Especialmente el cemento y también en menor medida algunos tipos de áridos contienen grandes cantidades de hidróxido de calcio [Ca(OH)2].
El agua es el vehículo de transporte de esta y otras sustancias. Por ello durante el fraguado o posteriormente cuando llueve o hay humedad ambiental o de los soportes es arrastrado a la superficie.
Allí, con el anhídrido carbónico del aire (CO2) forma el carbonato cálcico CO3Ca que es insoluble. El agua se evapora y este carbonato queda adherido a la superficie.
De forma lenta y según las condiciones ambientales, este carbonato con más anhídrido carbónico y humedad se va transformado en bicarbonato cálcico [(CO3H)2Ca] que por ser soluble se desprende fácilmente. Luego este será un problema temporal.
Evidentemente, en zonas con poca lluvia la transformación del carbonato cálcico en bicarbonato será más lenta que en zonas lluviosas.
CO2 + Ca(OH)2 –> CO3Ca + H2O
CO3Ca + CO2 + H2O –> (CO3H)2Ca
Cuando urge eliminar las eflorescencias, se puede recurrir a un suave lavado ligeramente ácido p. e. con ácido clorhídrico muy diluido. Este ácido es el desincrustante más empleado para los cementos.
Como el manejo de este ácido es muy peligroso, es recomendable utilizar el preparado diluido para uso doméstico salfumán, que a su vez diluiremos en torno a una parte de salfumán por 6 u 8 de agua. Con ello evitamos que el ataque sea demasiado agresivo y termine eliminando la lechada coloreada que envuelve al árido. Inmediatamente se procede a un abundante lavado con agua para retirar los restos de ácido.
En este caso, se forma cloruro cálcico que es más soluble.
CaCO3 + 2 HCl -> CaCl2 + CO2 + H2O
Evitar las eflorescencias por completo es muy difícil, pero sí podemos reducir su impacto actuando:
- Sobre el agua que es el vehículo transportador y
- Sobre el hidróxido cálcico que es el germen a partir del cual se forma la eflorescencia.
A.- Actuaciones sobre el agua para reducir las eflorescencias
Una primera medida es reducir el agua de amasado tanto como sea posible. En este menester nos serán de gran ayuda los aditivos plastificantes o reductores de agua.
Otra medida importante es dificultar los flujos de agua líquida por el interior de la pieza de hormigón. Esto se puede conseguir mediante la adición de sustancias hidrofugantes tales como los estearatos. Al actuar como repelentes del agua, bloquean la red capilar, y el agua no logra transportar a la superficie el hidróxido cálcico. Será de esta manera poca la cantidad de agua que en forma líquida atraviesa el hormigón. Otra parte de agua abandona la pieza en forma de vapor, en cuyo caso no hay transporte de hidróxido cálcico. Este aditivo incorporado a la masa tendrá beneficios tanto para las eflorescencias primarias como para las secundarias.
Adicionalmente podemos dificultar los flujos de agua líquida de cara a las eflorescencias secundarias aplicando un recubrimiento superficial a base de resinas o de sustancias hidrorepelentes como los siloxanos. Normalmente solo se recubren las partes vistas de las piezas, aunque otras veces se recurre a una inmersión completa de la pieza o del palet de piezas.
En el caso de las resinas conviene saber que estas alteran el aspecto al aportar brillo, sobre todo si en lugar de mate se opta por utilizar las satinadas.
Se tendrá en cuenta que los recubrimientos superficiales se degradan con el tiempo, especialmente si están expuestos al sol, por lo que periódicamente tienen que renovarse.
La mayoría de revestimientos se aplicarán cuando las piezas estén secas, es decir 24 horas o más después de la fabricación de la pieza.
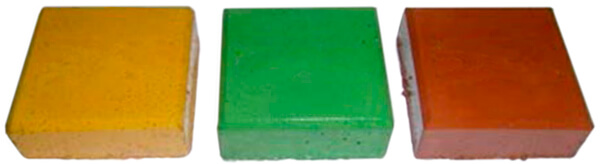
Aspecto de piezas de hormigón de colada con revestimiento superficial de resina base disolvente satinada.
Aspecto de piezas de hormigón de colada con revestimiento superficial de resina base disolvente satinada.
Algunos tipos de resinas de emulsión pueden aplicarse con el hormigón fresco, lo que ayuda a sellar los capilares durante el fraguado, actuando también así positivamente frente a las eflorescencias primarias.
También la red capilar del hormigón será más restringida en un producto muy compacto que en otro poroso, y por tanto, el agua tendrá más dificultades para desplazarse. Por ello, en la medida de lo posible se optará por una curva granulométrica de los áridos bien estudiada con el fin de conseguir la menor porosidad posible.
Evitando las corrientes de aire, también reducimos las eflorescencias. Las corrientes de aire tienen un efecto de succión en la superficie del hormigón, y por tanto tienden a aumentar el caudal de agua que circula por el interior del hormigón. Por otro lado, la renovación de aire proporciona la cantidad de CO2 que es necesario para formar los depósitos. En este sentido, se ha mostrado eficaz la cobertura de las piezas con film o bolsas de plástico durante el fraguado procurando que las gotas condensadas que se forman no caigan nuevamente sobre las caras vistas de las piezas, ya que dejarían manchas.
El fraguado en cámaras de secado es beneficioso para mitigar las eflorescencias. En dichas cámaras existen unas condiciones de saturación de humedad. Esto tiende a igualar la humedad dentro y fuera de la pieza de hormigón y por tanto los flujos de agua transcurren tan lentos que el transporte de hidróxido de cálcico a la superficie es muy bajo.
Fraguado en clima muy frío deja abiertos los capilares mucho tiempo, con lo que hay más oportunidades para las reacciones químicas que generan las eflorescencias. Acelerantes de fraguado ayudarán en este caso.
Por otro lado, en clima caluroso extremo o con exposición directa al sol durante el fraguado, el diferencial de humedad relativa es tan grande entre la pieza y el aire en contacto con ella que para equilibrarse el hormigón tiene una exudación violenta con gran arrastre de hidróxido cálcico a la superficie. El secado rápido de la superficie del hormigón bloquea prematuramente los capilares, sin embargo, las tensiones ocasionadas producen microfisuras que no hacen sino permitir grandes vías de salida de agua.
B.- Actuaciones sobre el hidróxido cálcico para reducir las eflorescencias.
Añadir al hormigón algunos materiales inorgánicos tales como puzolanas. Estas se obtienen habitualmente de forma sintética a través de subproductos de otros procesos industriales. Es fundamental que tengan estructura amorfa, lo que proporciona mayor reactividad con algunos componentes del cemento.
Las más utilizadas son:
- Cenizas volantes. Se trata de un subproducto de la combustión del carbón mineral. Es por tanto un residuo de las centrales térmicas de carbón.
- Humo de sílice. Subproducto originado en los hornos eléctricos de arco en la reducción del cuarzo para la obtención de silicio y ferrosilicio.
- Escoria de alto horno. Subproducto de la producción de materiales férricos.
La composición de la puzolana debe ser superior al 70% en SiO2 + Al2O3 + Fe2O3. Adiciones de estos productos, aparte de otros beneficios para el hormigón, reducen la formación de eflorescencias primarias, ya que estos productos reaccionan con el hidróxido cálcico en presencia de agua, es decir, durante el fraguado, formando compuestos insolubles que quedan alojados en el interior del hormigón. De esta manera se reduce la cantidad de hidróxido cálcico libre que con el agua llega a la superficie de las piezas.
2.– DESTONIFICACIÓN
Los productos a base de cemento, independientemente de que vayan pigmentados y de que hayan empleado cemento blanco o gris, tienen un proceso natural de amarilleamiento que termina estabilizándose después de varios meses. Este efecto es menos notable en los productos pigmentados.
Aparte de lo anterior, no hay que confundir la destonificación fruto de una descomposición del pigmento con la migración y fuga de este ni con el desgaste o erosión superficial de la pieza pigmentada.
- Destonificación por descomposición del pigmento. Este puede ser el caso del azul de ultramar, que en determinadas circunstancias se transforma en otro compuesto blanquecino.
- Destonificación por migración del pigmento. El caso más común es el de las piezas pigmentadas con negro de humo. El pigmento es estable, pero de tamaño tan pequeño que logra desplazarse por el interior de la estructura del hormigón hasta llegar a la superficie y abandona finalmente la pieza.
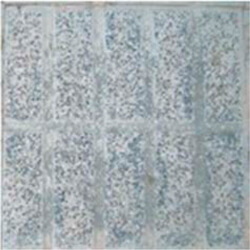
Baldosa hidráulica para exterior que fue pigmentada con negro de humo. Después de varios años, el pigmento prácticamente ha desaparecido.
- Destonificación por erosión superficial de la pieza. Deberíamos hablar en este caso de “falsa destonificación”, ya que en realidad lo que ocurre es la eliminación de la lechada pigmentada que cubre al árido, quedando este parcialmente al descubierto. De esta manera aflora una cantidad de puntos que van aumentando de tamaño y cuyo color es el del árido utilizado.
Veamos la evolución del aspecto visual de un suelo de un muelle de carga en diferentes zonas de este, ejecutado en el exterior, acabado fratasado. Pigmento utilizado: Rojo ChromaFer 1535.
Destonificación por erosión superficial
![]() | Zona no sometida a rodadura y preservada de la suciedad. El color del pavimento no se ha manchado con los neumáticos. El tono rosáceo corresponde a la combinación del rojo con una veladura de eflorescencias. |
![]() | Zona no rodada y sometida a la suciedad de diverso origen. Parte de esta suciedad corresponde al negro de humo de los neumáticos. El caucho va cediendo suciedad y negro de humo al suelo, que por su porosidad y absorción modifica su color. Se ha perdido el inicial matiz anaranjado. Persiste la veladura de eflorescencia. |
![]() | Zona de rodadura con fricción de intensidad media. Por un lado, se ha producido un pulido superficial que intensifica el color. Esto es debido a la eliminación de la eflorescencia por el frote de los neumáticos. Se ha incrementado la tonalidad violácea al contener mayor cantidad de negro de humo cedido por los neumáticos. Cuando el desgaste empieza a eliminar la cubrición de lechada pigmentada sobre el árido de cuarzo, empiezan a aparecer puntos blanquecinos correspondientes a dicho árido. |
![]() | Zona sometida a intensa fricción. El grado de eliminación de la lechada coloreada que cubría el árido es muy elevado. La sensación óptica es de pérdida de coloración. |
X. LEGISLACIÓN
Actualmente es de obligado cumplimiento lo dispuesto en la norma UNE-EN 12878:2007 sobre “pigmentos para la coloración del materiales de construcción fabricados a partir de cemento y/o cal. Especificaciones y métodos de ensayo.” Los pigmentos destinados a colorear productos de cemento deben tener la certificación del marcado CE.
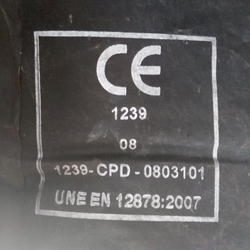
Llámenos y le ayudaremos en la correcta elección del pigmento ideal para sus necesidades. También puedes consultar información y productos relacionados con los pigmentos y colorantes visitando el siguiente enlace:
¿Te ha resultado útil esta información?… Si te ha gustado lo que has leído, nos encantaría que lo compartas con tus redes y que te unas a nuestra comunidad.
REFERENCIAS
[1] Guillamón, J.A., Pigmentos y Colorante, conceptos que a veces se confunden. G&C Colors, S.A.,. 2012[2] García Castán, J y Pérez Bustín, C. Color y Colorimetría. A.E.T.E.P.A., 1999.
[3] Gunter Buxbaum, Industrial Inorganic Pigments. Wiley_VCH. 1995
[4] Cornell, R.M. y Schwertmann, U. The Iron Oxides. VCH. 1996
[5] Guillamón, J.A. Los negros de humo para cementos, morteros y hormigones. G&C Colors, S.A.,. 2013.
[6] Carli Félicien. Les Ocres, comment et où les produit-on ?. Les cahiers de Terres et couleurs, 2010.
[7] Winkler, J., Dispersing Pigments and Fillers. Vincentz, 2012.
[8] Calavera Ruiz, J., Fenández Gómez, J., González-Isabel, G., López Sánchez, P. y Pérez Luzardo, J.M. Aspectos viuales del hormigón. INTEMAC. 2000
[9] G&C Colors, S.A., Documentación técnica.